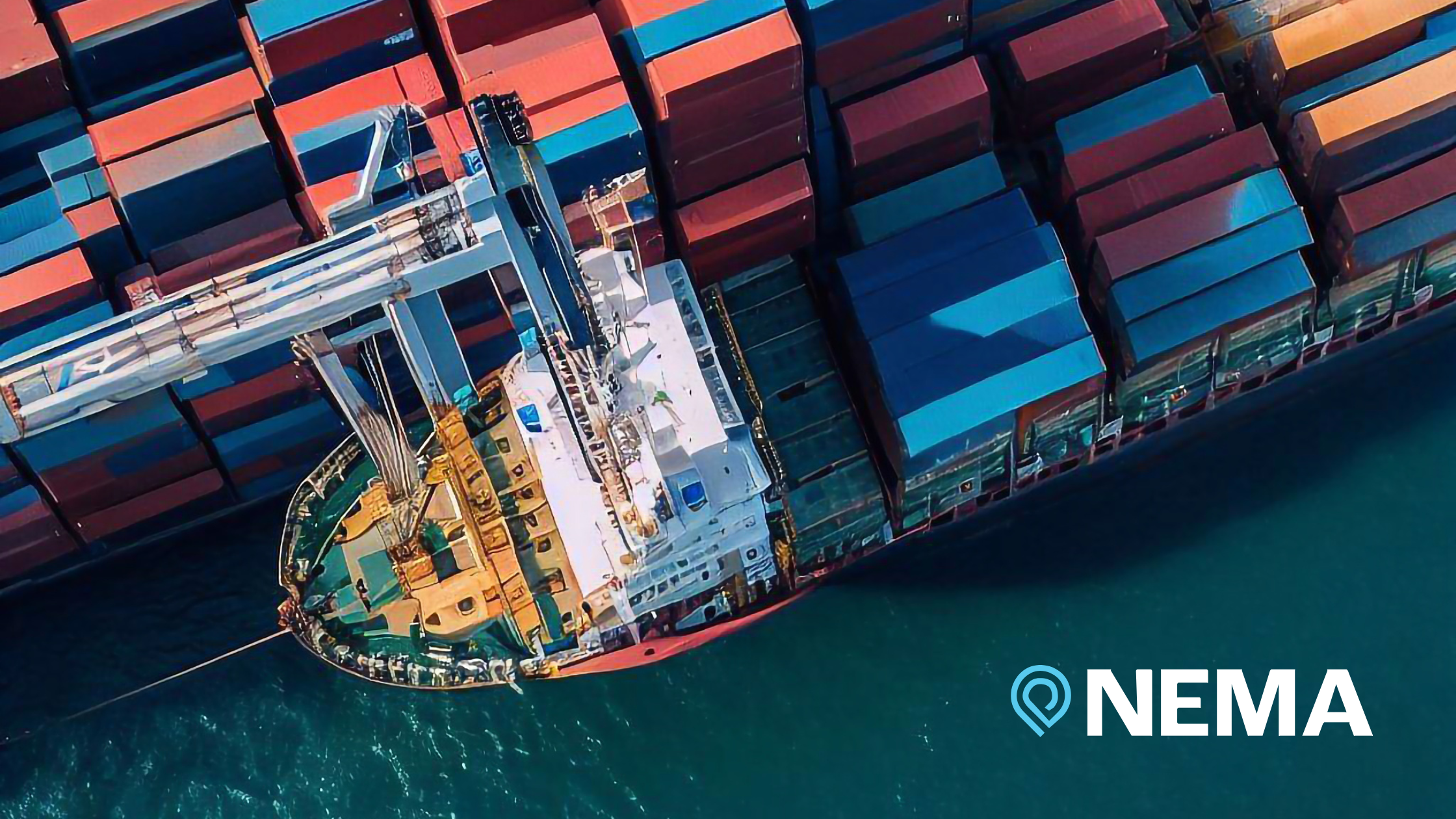
In October, a port labor strike stopped work at 36 ports along the East Coast of the US. The 47,000 longshoremen were only off work for three days, but in that time, delays began piling up, the cost of shipping containers increased and shortages on store shelves started to appear.
In November, Montreal longshoremen went on strike. While the effects of this aren’t substantial for our economy, it does draw attention to the fact that port strikes are becoming more frequent.
How to prepare your business for a port strike
Don’t be caught off guard if the tentative agreement that brought the longshoremen back to work falls through in January when it’s set to expire. Get ahead of any challenges this may bring to your business by planning ahead.
- Bring goods in from overseas now. Order inventory to bring in before January in case delays occur again. Even in the event of a brief port labor strike, the goods you need could be stuck in the port for weeks. Also, container prices will be lower now than they will be if another strike takes place. Importing product now can save you time and money.
- Consider warehousing: If you don’t have space for additional inventory, reach out to a warehousing partner like NEMA. Warehousing allows you to store excess goods that you may not have room for at your facility. Warehousing with us means your goods are securely stored and managed so they are available when you need them. We have 152,000 square feet of secure, cost-effective warehousing space.
- Take advantage of Foreign Trade Zone (FTZ): NEMA maintains the only 3PL FTZ in Gwinnett County, Georgia. We have easy access to the ports of Savannah and Charleston, both of which were affected by the strike, so if you take advantage of FTZ benefits now, you’ll be even farther ahead of the competition in the event of another port strike. You can still defer duties and enjoy other strategic benefits of utilizing an FTZ.
Why automation is important to supply chain logistics
Supply chain logistics is complicated and layered. We understand that to manufacture one product, you may be sourcing raw materials from multiple countries. Having each resource arrive on time and for the amount you expect is just one piece of the puzzle. That’s why our
team works to streamline and automate logistics. We partner with you to take the guesswork out of the process to save you both time and money.
- Inventory management: Inventory plays a crucial role in supply chain logistics. Knowing how many finished goods you have on hand versus ones in transit or production can help you determine the next steps in sales strategies and long-term planning. Systems that scan pallets and boxes, logging them into trucks or warehouses ensure accuracy for inventory management.
- Access to goods: Releasing inventory has never been easier than with automation that allows you to control the location of your goods with a few simple clicks. Our customers benefit from online access any time of day or night, giving them peace of mind and creating efficiency in their supply chain management.
- Tracking tools: We know that knowledge is power. Which is why our online tracking tools are easy to use and available 24/7 online. Simply log into your account to track shipments. Online tracking tools are just one element of supply chain logistics automation that can help you stay ahead of your competition, especially in times of crisis.
With strategic planning, you can avoid costly challenges to your business in the event of supply chain interruptions like a port strike. Choosing a dedicated and knowledgeable logistics partner can be the difference between driving toward success or making a wrong turn. Interested in learning more about the NEMA team and supply chain management process? Contact us today. We look forward to giving you room to grow.